Functional Prototype: Bridging Ideas and Reality
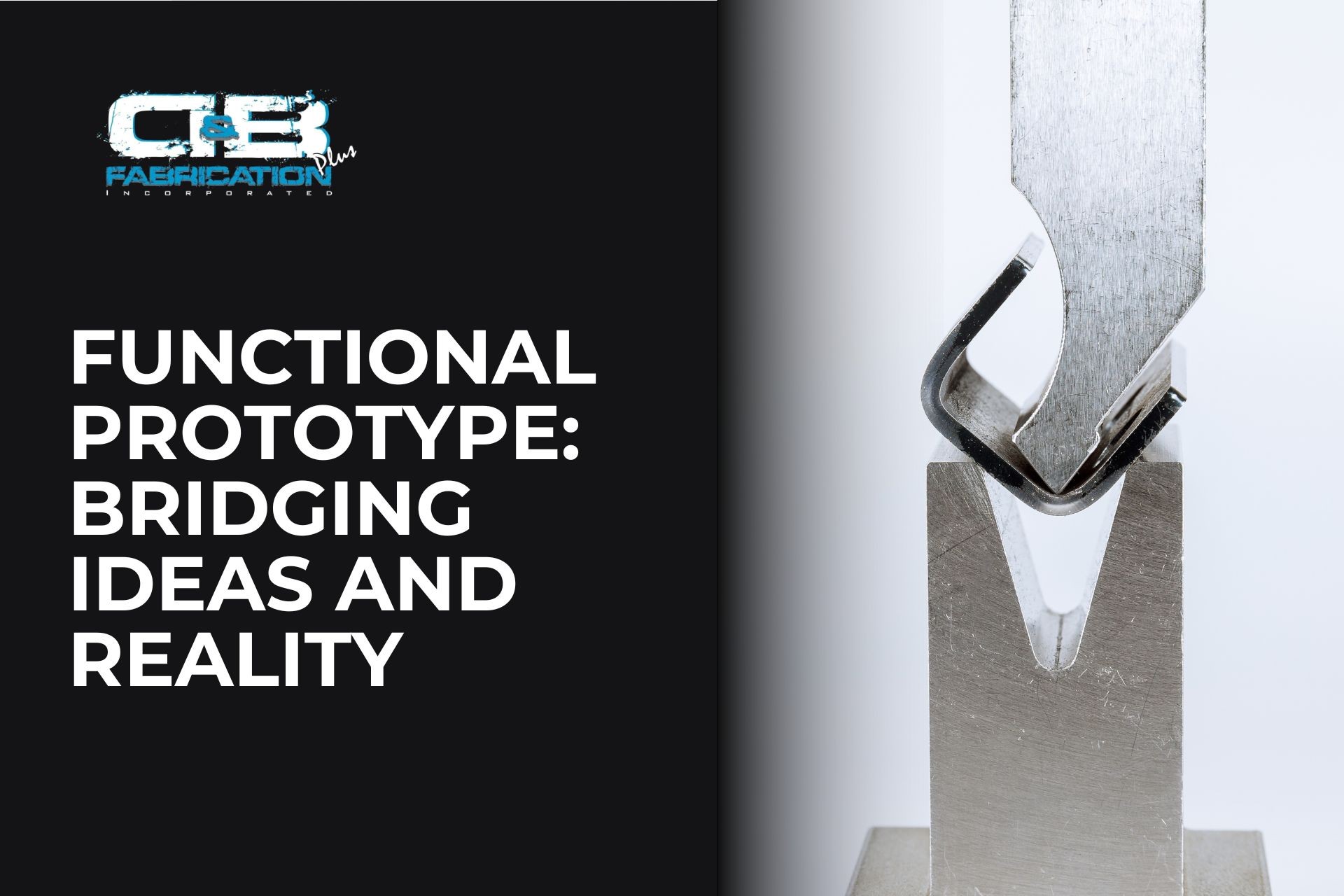
In product development and manufacturing, transforming a concept into a tangible, working model is a critical step. This transition is achieved through the creation of a functional prototype, which allows businesses and designers to test and refine their products before mass production.
A functional prototype is more than just a visual representation—it serves as a fully operational version of a product, enabling stakeholders to evaluate its performance, design, and usability. This comprehensive guide explores the importance, types, and process of developing a functional prototype and why it’s a cornerstone in innovative product design.
What is a Functional Prototype?
A functional prototype is a working model of a product designed to test its features, usability, and performance. Unlike aesthetic or conceptual prototypes, a functional prototype is built to operate similarly to the final product.
It allows designers, engineers, and stakeholders to analyze how the product will function in real-world scenarios and make necessary adjustments before full-scale production begins.
Functional prototypes bridge the gap between conceptual ideas and market-ready products. They are essential for identifying design flaws, improving performance, and ensuring that the final product meets user expectations.
The Importance of Functional Prototypes in Product Development
Developing a functional prototype offers numerous advantages throughout the product development lifecycle. These benefits include:
1. Design Validation
Functional prototypes allow teams to validate design concepts by testing how the product performs in real-world situations. This stage helps identify design flaws and areas for improvement, ensuring the product aligns with user needs and performance standards.
2. Cost and Time Efficiency
By detecting and addressing potential problems early, functional prototypes can save significant time and money. Making adjustments during the prototyping stage is far less costly than correcting errors after mass production.
3. Risk Reduction
Testing a working model reduces the risk of product failure in the market. A functional prototype ensures that the product functions as intended and meets safety and quality standards.
4. Enhanced Communication
Prototypes serve as a tangible representation of the product, facilitating clearer communication among design teams, stakeholders, and potential investors. This improves collaboration and decision-making throughout development.
5. User Feedback Integration
By allowing end-users to interact with the prototype, companies can gather valuable feedback to refine the product’s functionality and design, ultimately enhancing user experience.
Types of Functional Prototypes
There are several types of functional prototypes designed to meet different testing and development needs. Understanding these variations can help determine which prototype best suits a product’s development stage.
1. Low-Fidelity Prototypes
Low-fidelity functional prototypes are basic, simplified versions of a product. They are often constructed using inexpensive materials to test basic functionality and design concepts. These prototypes are useful for early-stage testing and rapid iterations.
2. High-Fidelity Prototypes
High-fidelity prototypes closely resemble the final product in terms of materials, functionality, and appearance. They are used for in-depth testing of product performance and user experience, providing a more accurate representation of how the product will operate.
3. Alpha Prototypes
An alpha prototype is the first version of a product that incorporates all intended features. It is primarily used for internal testing to identify design and engineering issues before external testing begins.
4. Beta Prototypes
Beta prototypes are more refined and are often shared with select customers or external testers for feedback. This stage is crucial for gathering real-world user insights and making final adjustments.
5. Rapid Prototypes
Rapid prototyping involves quickly creating a functional prototype using technology like CNC machining. This method accelerates the design process and allows for swift iterations and testing.
Materials and Technologies Used in Functional Prototyping
Choosing the right materials and technologies is essential when developing a functional prototype. The choice depends on the product’s complexity, function, and intended market. Common materials and technologies include:
1. CNC Machining
CNC machining is used for creating durable and precise prototypes from metals, plastics, and composites. This method is ideal for prototypes that need to withstand mechanical testing or mimic the final product’s strength.
2. Injection Molding
For products requiring plastic components, low-volume injection molding can produce high-fidelity prototypes. This method is useful for evaluating product performance in conditions similar to mass production.
3. Sheet Metal Fabrication
For industrial and mechanical products, sheet metal fabrication provides robust and accurate prototypes. This method is ideal for testing products that require structural integrity.
4. Electronics Integration
For products with electronic components, integrating circuit boards and sensors into a functional prototype allows teams to assess electrical performance and software compatibility.
The Functional Prototyping Process
Developing a functional prototype involves several stages, each critical to refining and validating the product. The typical process includes:
1. Concept Development
The first stage involves brainstorming, sketching, and creating digital models of the product. This step establishes the product’s design, features, and functionality.
2. Design and Engineering
Using CAD (Computer-Aided Design) software, engineers create detailed 3D models that specify dimensions, materials, and assembly instructions. This stage bridges the concept and prototype phases.
3. Prototype Fabrication
At this stage, the functional prototype is physically created using methods like CNC machining, or sheet metal fabrication. The choice of method depends on the product’s complexity and testing requirements.
4. Testing and Evaluation
The prototype undergoes rigorous testing to assess its performance, durability, and usability. This stage identifies any flaws or areas for improvement.
5. Refinement and Iteration
Based on testing results, the design is refined, and new iterations of the prototype are produced as needed. Multiple rounds of testing and modification ensure the product meets desired specifications.
6. Final Validation
Once the prototype meets all functional and performance standards, it is validated for mass production. This final step ensures the product is ready for manufacturing and market launch.
Applications of Functional Prototypes Across Industries
Functional prototypes play a critical role across various industries. Their applications include:
1. Automotive Industry
Car manufacturers use functional prototypes to test vehicle components, safety features, and performance. Prototypes allow for early detection of design flaws and help streamline production.
2. Aerospace Industry
In aerospace, prototypes are essential for testing aerodynamics, structural integrity, and safety systems. High-performance materials and precise manufacturing are crucial at this stage.
3. Consumer Electronics
Tech companies develop functional prototypes to evaluate product interfaces, battery life, and durability. This process is key to delivering user-friendly and reliable products.
4. Medical Devices
Medical device manufacturers rely on functional prototypes to ensure safety, efficacy, and compliance with regulatory standards. Prototyping enables rigorous testing before clinical use.
5. Industrial Manufacturing
In industrial manufacturing, functional prototypes help refine machinery, tools, and equipment. They ensure products meet performance standards before large-scale production.
Why Choose D&B Fabrication Plus Inc. for Your Functional Prototype Needs?
At D&B Fabrication Plus Inc., we specialize in turning innovative ideas into reality. With extensive experience in custom fabrication and precision manufacturing, we provide comprehensive functional prototype services tailored to your industry and product requirements.
Our state-of-the-art facilities and skilled team ensure that every prototype we produce meets the highest standards of quality and performance.
Our Expertise Includes:
- Advanced Fabrication Techniques: Utilizing CNC machining, sheet metal fabrication
- Material Versatility: Working with metals, plastics, and composites for optimal functionality.
- Customization: Tailoring each prototype to meet your specific design and performance needs.
- Comprehensive Testing: Ensuring every prototype functions flawlessly through rigorous testing.
Get Your Functioning Prototype Built at D&B Fabrication Plus Inc.
Ready to bring your product ideas to life? Trust D&B Fabrication Plus Inc. for high-quality functional prototype development.
Contact us today to discuss your project and discover how our expertise can help you innovate with confidence.